Last updated: 03.01.2024
Lean Management places great emphasis on eliminating problems that can cause waste. When does a company lose out? During downtime, overproduction, or during overstocking. With this management concept, a manufacturing plant can identify and eliminate these items, while emphasizing process optimization and reducing lead times. For employees to operate even more efficiently, the management system should also focus on improving the flow of information, its transparency and accountability.
In Article:
- What is the effective functioning of an organization? It's primarily about effective team management and process optimization.
- Looking for answers on how to achieve this, companies are increasingly focusing on the concept of Lean Management.
- The strategy is aimed at improving the quality and profitability of the company's production.
- These activities increase the company's competitiveness against the competition.
- What is Lean Management really? How do you introduce this strategy to your team? Read on and see how to increase productivity today.
Table of Contents:
- What is Lean Management? Basics of the concept
- Support in team management
- How to introduce Lean Management - steps for introducing the strategy
- How to monitor and measure performance after Lean implementation?
- Concerns about implementing this management strategy in the team
See also: How to do Lean without forcing people to Lean
What is Lean management? Basics of the concept
The basic premise of the Lean Management concept is to maximize the value a company gives to its customers. In doing so, it is a philosophy combined with a set of principles aimed at eliminating possible losses. It allows a company to reduce the time it takes to complete tasks, increase the efficiency of processes, as well as reduce costs and increase the quality of the final product. Lean management is responsible for creating a culture within an organization that leads to continuous improvement. In doing so, it indicates the importance of the role of employees in improving processes within the company.
Lean Management places great emphasis on eliminating problems that can cause waste. When does a company lose out? During downtime, overproduction, or during overstocking. With this management concept, a manufacturing plant can identify and eliminate these items, while emphasizing process optimization and reducing lead times. For employees to operate even more efficiently, the management system should also focus on improving the flow of information, its transparency and accountability.
Lean management support in team management
Central to the concept of Lean Management is team management. Its effectiveness is based on engaging and motivating employees. It is the leader's responsibility to support them during process improvement and create an environment that fosters innovation and continuous development. It is through the involvement of the entire team that an organization can achieve greater efficiency and effectiveness.
To successfully introduce a Lean Management strategy to a team, a leader needs to be conscious of the strategy and meticulous about planning. It is also important to educate employees about Lean Management. This will make them more willing to contribute in identifying areas for improvement, setting goals and monitoring progress. To automate this entire process, it is worth using tools such as a suggestion system.
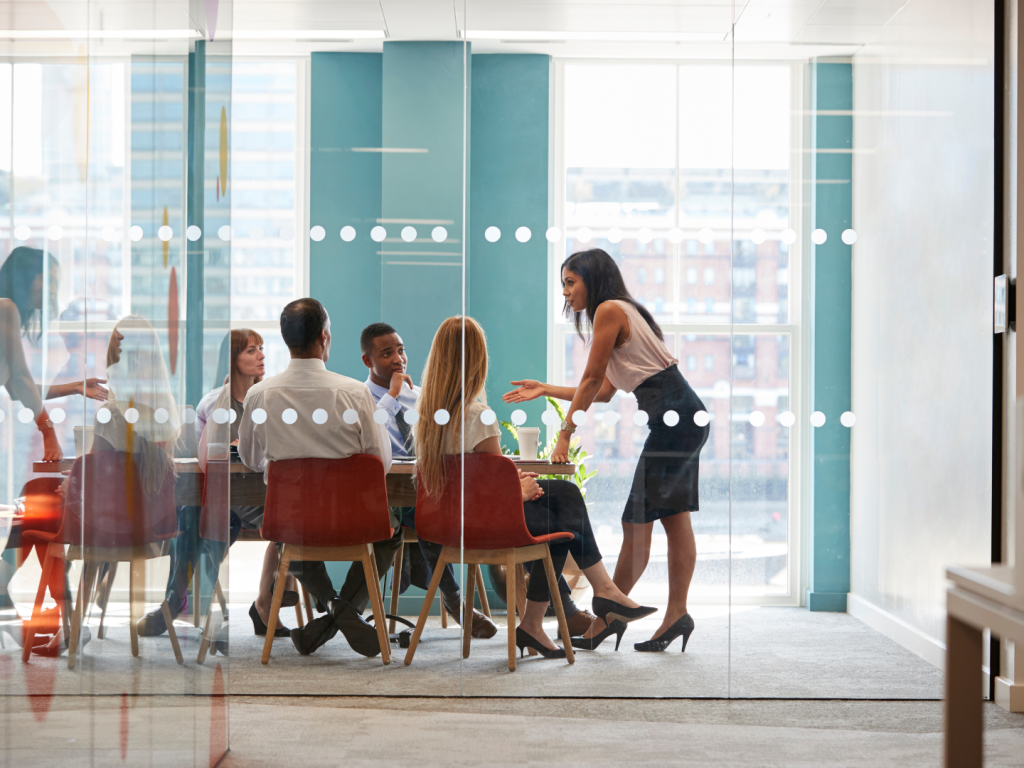
Companies that successfully apply Lean Management
Many companies around the world have successfully applied Lean Management for years. Among the forerunners of this philosophy is Toyota. It was on the foundations of its management that the whole concept of Lean Management was created. It created an entire strategy, which it called the Toyota Production System. It is based on Lean principles. Toyota's production system is not isolated in the manufacturing market. Among the companies applying the concept of Lean organization, we can also find Amazon, Nike or Boeing.
Lean and Kaizen - a combination of philosophies
Kaizen philosophy is a Japanese concept meaning continuous improvement. It is closely related to Lean Management and is a key element of the overall strategy. Kaizen focuses primarily on engaging all members of the organization to identify and eliminate bottlenecks and continuous improvement.
Does Kaizen effectively affect team management?
Kaizen positively affects the results of team management. This is all thanks to the organization of an environment that fosters innovative ideas and cooperation. Kaizen influences the development of employees' competencies, and this translates into the efficiency of team management and the achievement of better results.
How to Introduce Lean Management
- steps to introduce a strategy
How do you introduce Lean Management to your team in a practical way? It requires proper planning and implementation. At the very beginning, the most important things are:
- Analysis,
- Identification of areas for improvement,
- Lean Management training for the team.
Analysis and identification are aimed at checking the processes that the team manages and, at the same time, identifying bottlenecks, i.e. process elements that may cause problems or waste. By knowing the problems, we can prevent them and react faster when they occur. This stage is called value stream mapping. During value stream mapping, we can eliminate all activities in the process that do not add value for the customer, while generating costs, causing quality problems or production delays. Only a thorough understanding of the state of the process and visualization of the value stream will help to find the area for improvement and implementation of changes, which leads to lean management of the production process.
To put them into practice, it is necessary to take the next step to implement a business management strategy. Once you've mapped the current process and identified areas for improvement, it's time:
- Development of an action plan,
- implementing change.
These steps are aimed at preventing losses and organizational order at critical moments in the company's processes. Implementing Lean Management is all about planning how the team will behave in specific situations. A new value stream map is created in which all losses are minimized or even eliminated.
The final element of introducing Lean Management is to monitor progress and adjust strategies based on results.
How to monitor and measure performance after Lean implementation?
Once Lean Management has been introduced into an organization, it is important to monitor and measure its effectiveness. This is the only way to evaluate the effectiveness of the changes made and continue to improve. How to measure it?
Identify KPIs for your process
Identifying key performance indicators (KPIs) for a process is an important part of measuring the effectiveness of Lean management change implementation. These can include cycle time, quality, processing time, cost, error rate and others. Once you know what data is worth collecting and analyzing on a regular basis, you can use it to assess progress and identify further areas for improvement.
Kaizen and employees
Who to ask about waste and process improvement? Preferably people who witness events every day that can be improved. Encourage employees to submit their ideas and suggestions for improving work and eliminating waste. Monitor the quantity and quality of suggestions made by employees. Check regularly how many of these ideas have been implemented and how they have affected work efficiency.
Comparing results with previous periods
Comparing the results that are achieved after the introduction of lean management concepts to historical data or data from previous periods will allow you to assess the impact of lean management. By comparing results with previous periods, it is possible to see whether performance indicators have changed, costs have been reduced and processing times have been reduced.
Customer reviews
To find out if the Lean management method is working, it is worthwhile to survey customer satisfaction on a regular basis. Gathering feedback on the quality of products or services, as well as lead times or customer service can help measure the performance of Lean management in an organization. The customer's point of view before the strategy was implemented, and what feedback is received after the changes are made, are important indicators of how the concept is working.
Benchmarking as a method of measuring performance
Wanting to see how the changes made have affected the efficiency of the team, one can compare the results and performance indicators with other organizations that operate in the same industry and have also chosen to implement Lean Management tools. Such a comparison can provide valuable insights for the company to achieve operational excellence.
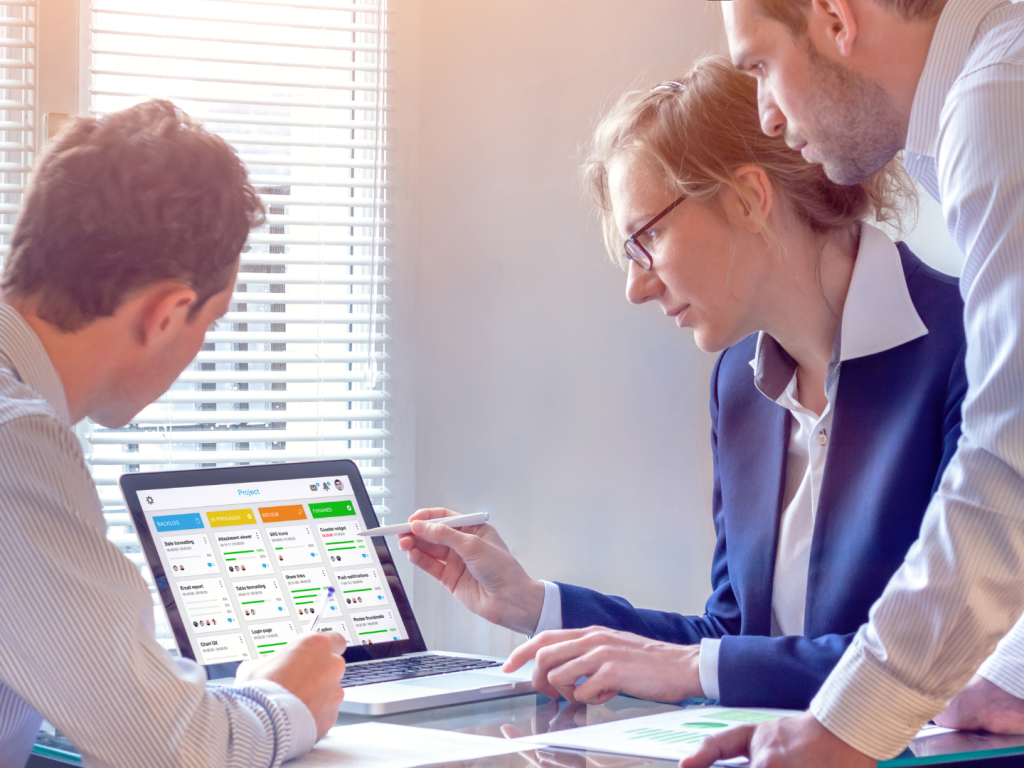
Concerns about implementing Lean Management in the team
The lean philosophy aims to streamline teamwork and minimize loss-making elements of the process. It is a way to increase competitiveness in the market created by management practitioners. However, implementing changes according to the method can cause fear and initial dissatisfaction on the part of both management and employees. Such internal rebellion is present whenever we intend to make a permanent change in the organizational culture.
This attitude arises in any company where we want to improve something that is, after all, working. Management is afraid of possible disruptions to the company's management system, and employees are afraid that it will take human effort to make changes. How to get rid of the fear of change? It is important to educate the team and make each member aware that the goal of Lean management is to streamline work and get rid of elements from the process that bring losses to the company.
Lean management is a concept that involves continuous process improvement. To know which part of the process is losing money, it is useful to involve employees in determining it. One of the principles of Lean management indicates that it is the team of employees that knows best what needs to be improved in the overall process. Does this mean that the leader has to ask each employee individually what ideas they have for improving the process? Of course not. One method is to use the tools suggested by Sherlock. This is the System Sherlock Waste, through which employees can make suggestions for changes they would make in their position. This system works well for both service and manufacturing companies.
Both Lean Management and Kaizen seek to improve both processes and employees. Both of these strategies, when introduced into a company, will help tailor the product to meet the growing expectations of customers in small steps. They make it possible to create a system that is friendly to both customers and employees. Minimize your company's losses using the means provided by Lean Management.
________________________________________
If your challenge is to engage employees in raising issues and suggestions for improving work and eliminating waste, monitoring the quantity and quality of suggestions made by employees, their implementation and impact on work efficiency, contact us, we know how to support your efforts: schedule a meeting>>.