lean management
Last updated: 13.03.2024
Focused on process optimization and employee engagement, the Lean Management strategy transforms team management into a more efficient and engaged process. This approach emphasizes the value of continuous improvement and collaboration, increasing employee motivation and satisfaction. Tools such as Sherlock Waste, support this strategy by making it easier to identify waste and initiate change, resulting in better performance and supporting the development of an organizational culture focused on continuous improvement.
Introduction: The importance of Lean Management in today's management
With increasing competition and the constant need for optimization, Lean Management has become a key component of many organizations' strategies. For senior managers, understanding and implementing Lean principles can be critical to achieving higher process efficiency and better team management. Systems such as Sherlock Waste can support this process by engaging employees in identifying and eliminating waste, which is key to a Lean strategy.
Lean Management is not only a management strategy, but also an organizational philosophy. It emphasizes continuous process improvement, streamlining workflows and maximizing customer value while minimizing waste. A key aspect of implementing Lean in a team is to develop the ability to recognize areas of inefficiency and continuously improve processes. The involvement of every member of the team is extremely important here, as it is employees at every level who can best see where and how the company's operations can be improved.
On the other hand, implementing Lean Management requires leaders to understand that it is a long-term process that requires patience and consistency. Success in this area is based on a culture of openness to change, continuous learning and cooperation between different departments of the organization. The key here is also to properly train and support employees in developing their problem-solving skills, and to allow them to have a real impact on the company's processes. Lean management is not just about tools and techniques, but above all a way of thinking and acting that should permeate the entire organization.
Table of Contents:
- Introduction: The importance of Lean Management in today's management
- What is Lean Management?
- Why is Lean important for your team?
- How do you implement Lean in your team?
- Benefits of Lean for team management
- Introducing Lean Management strategies to your team - summary
See also: Lean and Kaizen in Polish
What is Lean Management?
Lean Management is a management philosophy focused on maximizing customer value with minimal waste. This means identifying and eliminating any activities in processes that do not add value, while emphasizing continuous improvement, known as Kaizen. It is an approach that requires the involvement of the entire team and continuous process analysis.
Lean Management goes beyond management techniques alone - it is a holistic approach to running a business. It is based on a team's commitment to continuous process improvement. It is distinguished by a focus on customer value-added and waste reduction, which means eliminating any activities or process steps that are not beneficial. The basis of this system is a culture of continuous analysis and adaptation, which requires involvement at all levels of the organization, from managers to line workers. Every team member plays a key role in identifying opportunities for improvement and innovating.
Why is Lean important for your team?
Introducing Lean strategies into a team can bring many benefits. First, it helps identify and remove inefficient processes, leading to greater efficiency and better productivity. Second, it promotes a culture of continuous improvement, encouraging employees to think innovatively and proactively. Finally, Lean contributes to better employee engagement, as it gives employees a real say in shaping work processes.
Lean Management is essential for your team because it introduces efficiency and eliminates waste. By focusing on values that have a real impact on the customer, the team becomes more results-oriented. Kaizen's culture of continuous improvement encourages employees to be innovative and proactive. Every team member participates in the optimization process, which increases their commitment and sense of belonging. Lean implementation also improves communication within the team and contributes to better planning and resource management.
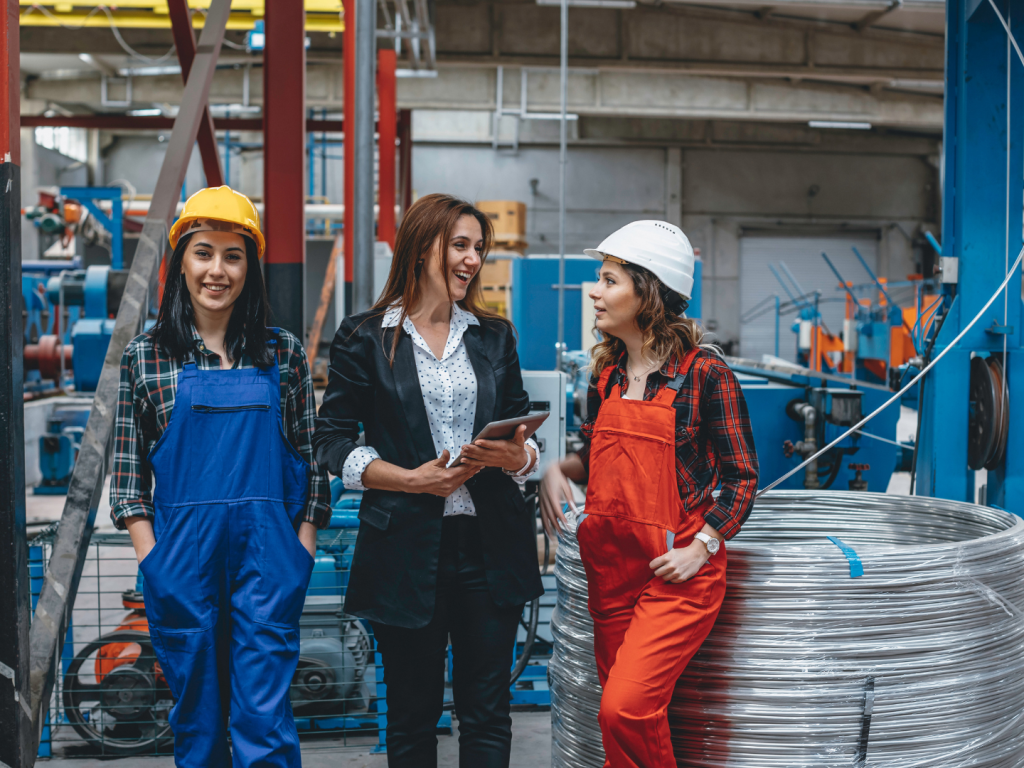
How do you implement Lean in your team?
Implementing Lean requires a strategic approach. Here are some steps that can help:
- Training and Education: providing training to the team on Lean and Kaizen principles is key. Employees need to understand what Lean is and how they can contribute to its implementation.
- Process Analysis: Conduct a detailed analysis of current processes to identify areas of waste and opportunities for improvement.
- Engaging Employees: Use tools such as Sherlock Waste, to encourage employees to submit their ideas for improvement.
- Implementing Change: Start by implementing smaller changes that can bring quick benefits, and then gradually make larger changes to processes.
- Monitor and Adjust: Regularly monitor progress and be ready to adjust strategies in response to feedback and results.
In summary, when implementing a Lean strategy in a team, training and educating employees on Lean and Kaizen principles is key. The next step is to analyze current processes to identify waste and opportunities for improvement. It is important to engage employees, such as through tools like Sherlock Waste, which encourage ideas for improvement. Implementation should start with smaller changes and then evolve to larger process modifications. It is also essential to regularly monitor progress and adjust strategies based on feedback and results.
Benefits of Lean for team management
The introduction of Lean Management can significantly affect the way a team is managed. Employees become more engaged and motivated, as they see that their opinions are important and have a real impact on company operations. In addition, Lean promotes clear communication and collaboration, which is key to effective team management.
Benefits of implementing Lean Management in team management include:
- Increased employee engagement through participation in process creation and improvement.
- Better communication and cooperation in the team, which translates into work efficiency.
- Increased motivation and job satisfaction as employees see the impact of their actions on company performance.
- Improved processes leading to higher productivity and better business results.
Introducing Lean Management strategies to your team - summary
Lean management strategy is not only a tool to optimize processes, but also a way to build a strong and committed team. For senior managers, understanding and implementing Lean can be crucial to an organization's long-term success. Tools such as Sherlock Waste can be a valuable support in this process, enabling effective employee engagement and continuous process improvement.
Focused on process optimization and employee engagement, the Lean Management strategy transforms team management into a more efficient and engaged process. This approach emphasizes the value of continuous improvement and collaboration, increasing employee motivation and satisfaction. Tools like Sherlock Waste support this strategy by making it easier to identify waste and initiate change, resulting in better performance and supporting the development of an organizational culture focused on continuous improvement.
__________________________
If your challenge is to manage your team effectively, focusing on process optimization with active employee engagement, see how modern technology Sherlock Waste can support you in this. Contact us: schedule a meeting >>