Are you a leader, a manager, a manager. Are you worried that everything is on your head? That all the innovations are you? That you are the only "engine" of the company? Take a look around. You have 10, 50, maybe more than 100 spare engines. So many that most of them, have never been fired up.
Eiji Toyoda, president of Toyota Motor Company, said more than 80 years ago: "One of the characteristics of Japanese workers is that they make use of their minds as well as their hands. Our employees make one and a half million suggestions a year and 95% of them are implemented." How did the West react? To put it mildly, with a contemptuous smacking of the lips. The first half of the 20th century was the time of so-called mass production. It was a time of tremendous social breakthrough.
Ford's brilliant innovation - mass consumption
Ford was the first to pay ordinary workers $5 an hour. Others paid less than a dollar. Did he have a good heart? Where else! This was the beginning of the era of consumption. For the first time, an ordinary worker was able to buy what he produced. Today this is the norm, one of the canons of the world economy.
"A worker is for doing and not talking". - resonated at a time when workers in mass production were illiterate, almost faceless, despised cogs in the machine. This kind of thinking, resulted in abysmal product quality. There were days when 100% of cars had to be repaired... before leaving the factory. But it still paid off. People bought like crazy, no matter what.
Toyota ups the ante
Toyota let the Corolla go to the World, after 10 years of production for internal use. They chose the date well. 1973. An economic crisis. People were looking for cheap cars, in place of highway cruisers. Corolla production absorbed millions of small ideas, thrown in by employees every day. A well-managed Employee Idea System had been in place for 10 years. The worker was from "thinking, talking and doing." He was taught standards copied dot for dot from... the Americans using the TWI method. Interestingly, the Americans used TWI during the war and abandoned the system shortly after the war ended.
The Corolla has conquered Western markets. But the biggest sensation was discovered by accountants. Toyota's income, after deducting all production costs and the cost of transporting cars halfway around the globe, was three times that of other auto giants. Simply put, employees helped the company eliminate waste, visible only to them.
Shinkansen
2018. I'm off to Japan in search of inspiration for innovative companies. What's it like at the source? I'm at Toyota. For the first time in my 20 years as a Lean consultant, I see a leader who is constantly on Gemba with employees. He observes. Sometimes he asks. He writes things down. I stand for 2 hours. He disappears once, for 10 minutes. He returns with a colleague and they discuss showing something on the line.
In Poland, "there is no time." With the most open I work to spend an hour a week like this.
Japan. We visit a small but very innovative company called Hiraoka Tools. They create prototype tools. Their official vision sounds strange: "Realizing the material AND spiritual happiness of Hiraoka Tools employees.
The chairman spends two hours with us.
- Why such a Vision?
- It's simple, only happy employees, make happy customers," he explains, " I'm just the main engine. Many companies work like a regular train. They run on one engine. We are like the Shinkansen.
- So fast?
- No, the Shinkansen has an engine in each wheel....
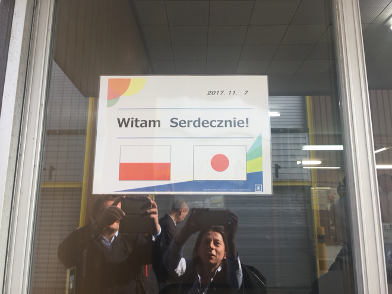
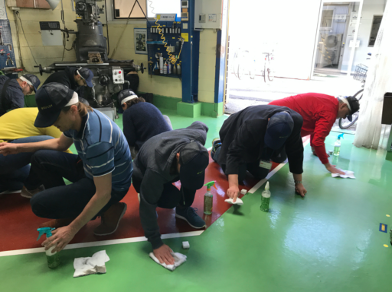
See Sherlock Waste in action!
- free presentation
- see the benefits in real terms
- we do not require credit cards